A lot of science and testing goes into a steel roofing product like LYSAGHT KLIP-LOK 700 HI-STRENGTH® so that it never becomes airborne, especially in a cyclone prone city like Townsville in North Queensland. However, on a recent high rise re-roof project completed on the exposed shoreline of this northern city, it proved to be a pre-requisite that the replacement steel roof sheeting could be made to "fly".
Used in this project
- Products
- LYSAGHT KLIP-LOK 700 HI-STRENGTH®
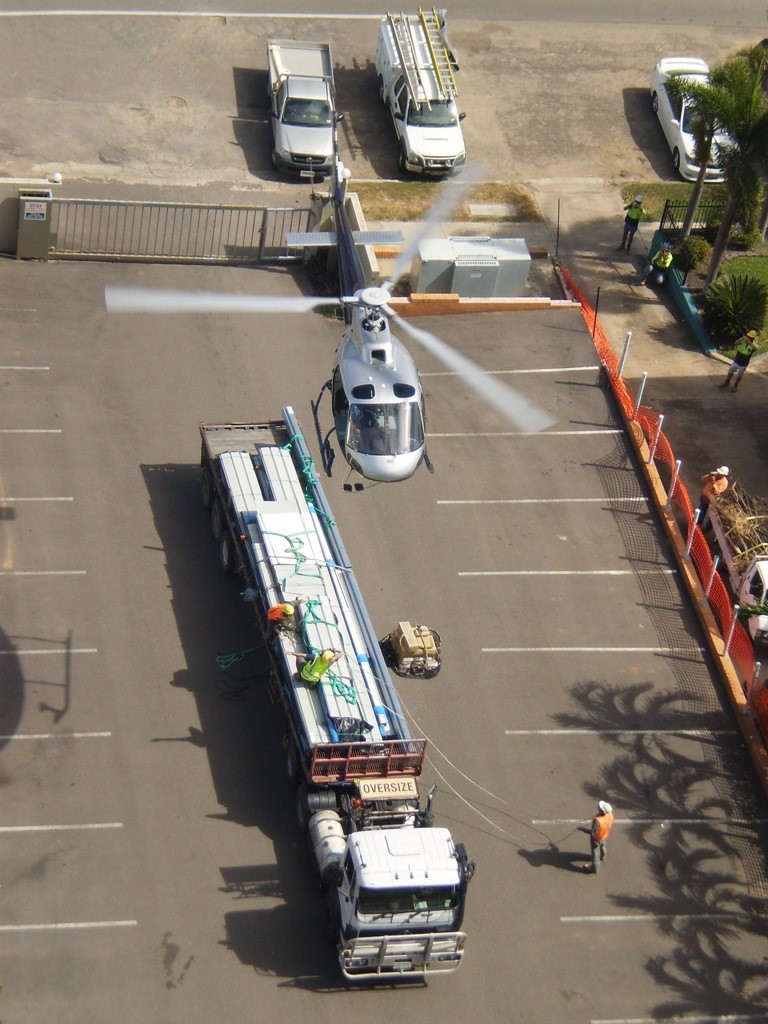
After 25 years of exposure in an aggressive marine environment, the original metal roof on the Aquarius building was showing signs of severe stress and had effectively reached the end of its service life. The logistical challenge was how to remove this old roof located 15 storeys above the ground and replace it with a new one. This task fell to local builder, Steve Wallace of SW Home Maintenance, employed by the Aquarius Body Corporate to manage the process.
"Initially it seemed like a nightmare scenario," Steve observed wryly, "and one that I had never encountered previously." At first he looked at setting up a crane jib boom but apart from the costs involved it would have meant taking up a lot of space in the building car park and causing inconvenience to tenants over a number of weeks.
Finally it was decided that the easiest and most economical way to get the job done was to employ a helicopter lift to "fly" the sheeting up onto the roof.
That meant a lot of prior arrangement with local authorities including council permits, traffic control, road closures and police presence, all of which had to be coordinated", Steve recalled. On the day it was important that the wind did not rise above 30 knots. "Also before the re-roof work could begin a couple of old evaporative cooling towers had to be removed from the roof by helicopter".
Going back a few steps, local engineer Pat Murray from Glynn Tucker Consulting Engineers had also been engaged to take a look at the existing roof structure and assess this in terms of wind loads and current engineering practices compared to those in vogue at the time or the original construction. "That had its own little set of challenges", Pat pointed out. The roof structure was originally constructed with a timber frame that had been fixed on top of a concrete slab. "The design had to be supplemented with additional support members including LYSAGHT® C15015 steel purlins as well as enhanced fixing methods to reinforce the structure so that it met the latest wind design loads", he said. All this work had to be subsequently inspected by this engineering firm prior to issue of a Form 16 for work completed.
The roof removal and replacement was undertaken jointly by two Townsville based roofing contractors, Don Hobson and Ian Sleigh, both experienced roofers and no strangers to working high above the ground in hazardous circumstances where knowledge and experience are paramount.
"It was quite easy really", Don commented nonchalantly, "once the method of lifting had been decided it was just like any other re-roof job for us".
"We installed safety barriers around the roof perimeter and blocked off the roof parapets with timber to make the work area safe", he added.
"We asked the steel roofing manufacturer, Lysaght, to pack the roof sheets in special pack sizes", Don said. "This was to comply with the maximum helicopter lift capacity of 450 kilograms", he explained. The packs also had to be securely strapped and separated by timber dunnage so that they could be easily lifted with slings off the back of a semi trailer on site. There was over 2 tonnes of LYSAGHT KLIP-LOK 700 HI-STRENGTH® roof sheeting involve with some sheet lengths as long as 10.7 metres. Also there was 1.5 tonnes of LYSAGHT® C150 purlins in 6 metre lengths. Delivery times had to coincide precisely with the lifting schedule so as no costly delays occurred with the helicopter.
"It was just a big team effort on the day", according to Ian Sleigh. Professional riggers were employed both on the ground and up on the roof by Townsville Helicopters to do all the attaching and detaching of slings to the bundles. Everyone else on site took their instructions during the lift from a dogman on the ground in direct two-way radio contact with the helicopter pilot."It all went off without a hitch", Ian added.
"It was all the contingencies that we had to plan for prior to the event that increased the stress levels for me personally", said builder Steve Wallace, "but the whole lifting exercise was over in two hours on the first day without incident". The helicopter was also employed again a few days later to remove the old roof and return it safely to the ground.
Reflecting later on this project, North Queensland Regional Manager for Lysaght Matt Hardy said, "The biggest concern from our perspective was not exceeding the maximum weight of each pack and the very limited timeframe available in which to perform the lift". The helicopter cost and time bound nature of the flight planning meant that arrival time of the roof on site had to be precise.
"The lift went with the precision of a Swiss watch", Matt added. "Regular communication between the key stakeholders both at planning stage and on the day was the key". Matt was also really proud of the way his Townsville Team made it happen.